
Features
Snow & Ice
Technology
How to prepare for a snow crisis and those ‘what if’ moments in snow removal
‘Boot camp’ gives snow contractors advice about how to deal with tricky scenarios
December 8, 2024 By Mike Jiggens
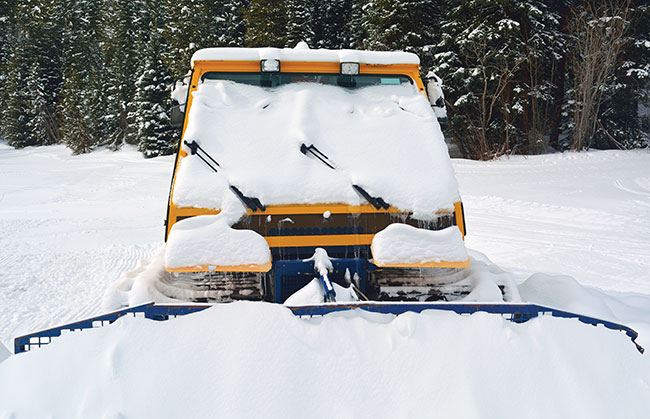
As professionals, snow contractors have developed a sound game plan when confronted by a significant snow or ice event. They’ve already done their equipment checks to ensure everything is in working order, they’ve made the necessary pre-season site visits to know where they can and can’t plow, and they’ve made sure their crews have been adequately trained.
With everything seemingly in order, there can still be unexpected setbacks that can put even the best-trained operators at risk. These “what if” scenarios should be addressed well before the first snowflake falls from the sky and they can avert a serious situation from occurring.
Health and safety consultant Matt Gehrich addressed the question – “What if your team gets stranded?” – during a virtual “Winter Boot Camp” session the Snow and Ice Management Association presented in October.
He noted there have been more weather extremes occurring in recent years than have ever been seen before, and, without the proper precautions, snow removal crews could find themselves caught in a dangerous and perhaps even life-threatening predicament.
Access to weather trends and forecasts is better today than it’s ever been, but tragedy can still occur, Gehrich warned.
“We need to use these technologies, but we can’t just assume or rely on the fact that that’s what’s going to answer our questions or solve our problems,” he said. “At the end of the day, we gather that information, and we use it, but it’s our situational area that’s going to matter.”
Gehrich said snow contracting businesses claim to be ready for whatever confronts them, but added there are “missing pieces” that must be addressed.
“It’s very easy to miss things,” he said, adding contractors must think “way outside the box” if they believe they’re prepared for every possible eventuality.
Winter weather hasn’t been constant over the past 20 years. Equipment has undergone modifications during that same time, and companies’ personnel have changed over the years. Gehrich suggested snow contractors shouldn’t get too comfortable or complacent, noting people are their greatest asset, and it’s a company’s operators who are most prone to the consequences of “what if” scenarios.
An operator might be dispatched to a remote location several kilometres from home base. A storm might leave eight inches of snow in the vicinity of the contractor’s depot, but the plow operator could be met with 14 inches at the job site located a significant distance away.
“Every inch changes the dynamic.”
Gehrich said the operator might become overwhelmed by the amount of snow he’s plowing and becomes stuck in a deep drift. As an experienced operator, he manoeuvres his truck back and forth, being careful not to burn out the transmission, but his efforts to free himself are futile. The driver gets out of the vehicle and attempts to dig himself out with an emergency shovel but is exposed to a temperature of minus 12 degrees Celsius and a wind speed of 32 kilometres per hour. Even though the operator is dressed accordingly, he’s unable to cope with the windchill. He gets back into his truck and tries to call for assistance but realizes the storm has knocked out cell phone service.
The driver is stuck in a remote area, has no means of communication and is amid freezing conditions. Gehrich said it’s a possible scenario contractors must think about. The situation could be worse yet, he added. The operator’s truck may not only be stuck but might have experienced a mechanical breakdown or has tipped over.
“What happens when the truck is disabled but to a point where there’s no using the truck anymore? Let’s say a fire breaks out under the hood.”
In such a “what if” scenario, the driver may have successfully extinguished the fire, but the electrical wiring has burned out, leaving the operator with no heat, no lights and no communication.
“Now we have a serious problem because the driver can’t even stay warm by the heat of the truck. Those are things that I believe are very real and they happen or have happened.”
Consider one’s physicality
Gehrich said the driver’s physicality must also be considered, offering another possible scenario. Perhaps his truck hasn’t broken down and he still has phone access, yet he might have suffered a heart attack or stroke, or he got out of the truck to clear snow or ice from his lights or windshield and slipped on ice, hitting his head and suffering a concussion.
“Remember, when your people get to the sites, they’re the first ones there. The site is the most dangerous when they get there. You can be dressed as warm as you want, but if you hit your head, you have a problem.”
An incapacitated driver is in serious trouble, even if he has adequate heat and cell phone service.
Snow contractors should make a list of “what if” situations and devise a Plan B, Gehrich advised. A backup plan might require “old school” technology.
He said in a situation where cell phone service is rendered unavailable or if an electrical problem knocks out GPS, walkie talkies will re-establish communications.
“The walkie talkies of today are far superior to what we ever used years ago,” he said, noting modern units can provide upwards of 50 kilometres of coverage. “It’s old fashioned, but it absolutely will work.”
Walkie talkies should be tested before an emergency arises, Gehrich said. He suggested an operator visit a remote job site on a day of favourable weather and communicate with a co-worker at the shop to ensure the range is good.
“Don’t wait until the time happens to find out that they don’t work. These are good ideas, but they’ve got to be tested.”
Gehrich said walkie talkies are relatively inexpensive but advised against buying cheap units that might not work as well as expected.
“It’s a minor insurance policy, if you will.”
A lack of communication can also be overcome by installing cameras on site. Service through Wi-Fi is the preferred option over cell service, he said, noting cell towers can be knocked down in severe storms.
“It (cameras) gives you the ability to see what’s going on so that you have these cameras throughout the site and especially in the back corners and loading docks where a camera up on a light pole may not be able to see. Make sure you have your areas covered.”

An operator who must get out of his truck to clear his windshield poses a threat to himself if the outside temperature and wind chill are more than he can bear.
Photo: wollertz/Adobe Stock
Go bags and other aids
Drivers should be equipped with “go bags” containing water, juice or a Gatorade-like product, and healthy food items such as granola bars, packaged nuts, fresh or dried fruit and protein meat sticks.
“The whole idea is if they get stranded, if they’re out there and something happens and maybe they’re out there for some extended period of time before somebody knows there’s a problem or somebody can get to them, that they’re going to need hydration and they’re going to need food to build energy in their bodies and keep them warmer.”
Air-activated foot and hand warmers can be stored inside a truck for use in an emergency. Gehrich said placing them inside a pair of boots or mittens when needed can stave off frostbite.
“Toes and fingers are very susceptible to frostbite. Give them a fighting chance.”
A fresh set of clothing, including extra gloves and hats, allows stranded operators to change into dry apparel. Gehrich suggested fluorescent clothing is better under such circumstances.
Other items such as phone chargers, road flares, thermal blankets and jumper cables are good to have on hand in an emergency. Gehrich said he’s seen many types of inferior jumper cables that have weak wiring that may not carry sufficient voltage.
“Don’t go cheap on things like that. Get the heavy-duty ones.”
Flare guns can make a significant difference when operators are stranded in remote locations with no means of communication.
“What if someone is a mile away? How are they going to know if you are in trouble and need help?”
Like fire extinguishers and other equipment, flares and flare guns need to be checked over on a regular basis to ensure they’re in proper working order.
A contractor’s employees can’t be overlooked, Gehrich said, noting their health is of utmost importance. They should be encouraged to undergo annual physical examinations and to live a healthy lifestyle, he added.
“In wintertime, the physical stress that’s on our people is tremendous.”
They may face similar challenges during the summer when temperatures are soaring, but winter-specific setbacks including frostbite and hypothermia can take their toll on those who are least prepared.
Gehrich suggested snow contractors make a visual inspection of their operators, looking for such signs as shortness of breath, if they’re holding their chest, if their eyes appear glassy or if they seem to be feeling off.
“If someone is already struggling and we put them behind the wheel of a 25,000-pound truck carrying salt, it’s not a good situation. Let’s take that extra step and add that to our list of making sure we’re doing as much as we can for our teams.”
This article is part of the Technology Week.This article is part of the Snow & Ice Week.
Print this page